Precision Molded. Quality Assured.
At Plastic Parts, Inc., quality is more than a checkpoint — it's a mindset, a system, and a promise that drives everything we do. We apply the same precision and discipline to our internal processes as we do to your parts: measured, monitored, and continually improved.
What the Numbers Say About Our Quality
We track and evaluate our performance with the same precision we apply to your parts. Our performance metrics speak for themselves:
0 PPM
Defect Rate
Proven Part Quality
Achieved for a key customer through validated processes and in-line quality control.
99%+
First Pass Yield
Built Right the First Time
Most parts pass inspection the first time, reducing rework, waste, and downstream delays.
Tolerances
up to ±0.001
Engineered for Precision
Consistent part accuracy, even in tight-tolerance and high-performance applications.
Precision Built In: From Mold to Material
High-quality starts long before the first shot is molded. At Plastic Parts, Inc., our precision manufacturing process takes a holistic approach, factoring in part complexity, material composition, mold and cavity design, and the end-use application. We operate within validated molding windows to maintain tight control and consistency, run after run. This approach allows us to build quality into every step of the process—not just inspect for it at the end.
- Cleaning and inspecting each mold after every run
- Using ultrasonic and fluidized systems to remove fine residue from delicate features
- Performing preventive maintenance to extend tool life and maintain dimensional accuracy
Every press is equipped with real-time monitoring, and our team conducts scheduled in-process quality checks tailored to each part's specifications. These quality checks enable early detection of variation, reduce downtime, and ensure repeatable results across all production runs.
Our level of process control, combined with deep material expertise and proactive mold care, forms the foundation for consistently high-performance parts.
Material Expertise for Demanding Applications
We don’t just mold plastic — we mold performance. Whether you're designing for heat, durability, or compliance, we help match the right resin to your part and process. Our team works with a wide range of high-performance and specialty resins carefully selected to meet stringent technical requirements.
We regularly process:
- High-temp materials: PEEK, PPS, PPA
- Filled & unfilled nylons: Glass-, carbon-, mineral-, and Kevlar®-reinforced
- Functional additives: Laser-markable, anti-microbial, flame-retardant, UV-protection
- UL-tested and custom-colored materials
Material selection is only one part of achieving optimal performance. The proper custom injection molding process plays an equally critical role. Here’s how our capabilities align with specific application needs:
Custom Molding Processes
Process | What We Do | Key Benefits | Ideal Application |
---|---|---|---|
Scientific Injection Molding | A data-driven, decoupled process that separates injection and packing stages | Ensures repeatability for complex or crucial parts | Tight tolerance, high-volume requirements, including regulatory/medical parts |
Insert Molding | Molds plastic around metal, ceramic, or other plastic components | Creates strong, unified parts with embedded functionality | Embedded electronics, structural inserts |
Overmolding | Encapsulates one part feature over another in a single process | Improves grip, comfort, and product aesthetics | Ergonomic handles, tactile features |
Gas-Assist Molding | Uses nitrogen gas to hollow out thick sections during molding | Reduces warpage, weight, and material usage | Large components with thick walls |
Plated Plastic Parts | Applies thin metal finishes for a decorative, corrosion-resistant finish | Delivers high-end look and conductivity options | Automotive trim, consumer electronics |
In-Mold Decorating/Labeling (IMD/IML) | Integrates labels or high-end graphics directly into the plastic part during molding using flat, curved, or 3D-formed films | Offers durable, high-impact decoration while eliminating secondary operations and adhesive-based labeling | Consumer-facing parts requiring branding, visual appeal, or surface protection |
Certifications & Compliance You Can Trust
Quality at Plastic Parts, Inc. isn’t just about what we make — it’s how we operate. Our processes are built for consistency, traceability, and continuous improvement. In addition to our internal standards, we work closely with customers to meet stringent regulatory and documentation requirements.
We actively ensure compliance with key global and industry-specific regulations. Our certifications and standards include:
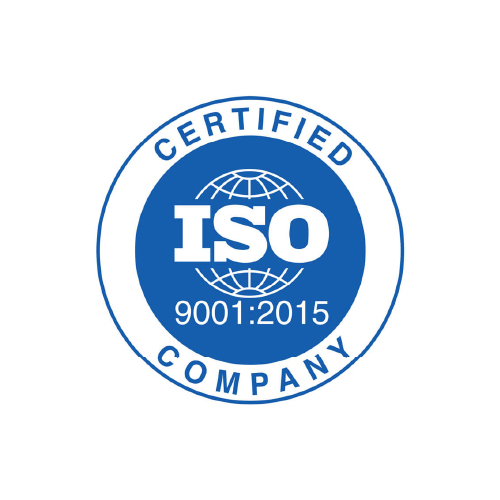
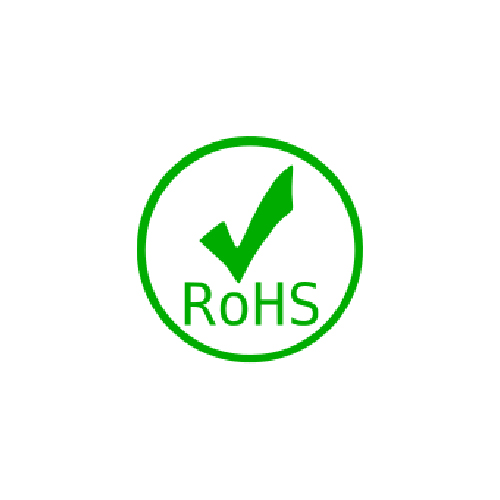
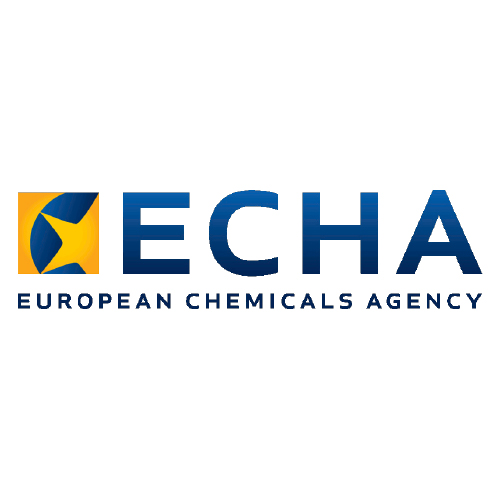
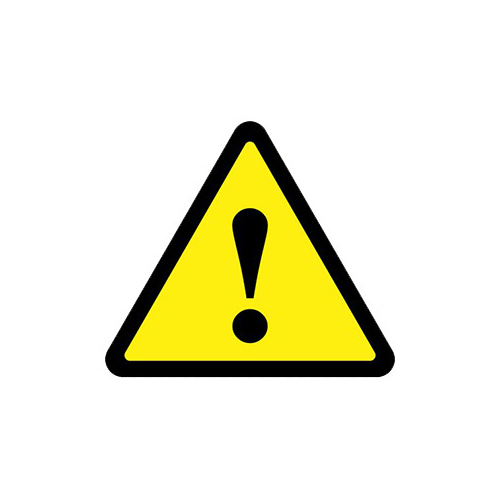
Precision Inspection, Powered by Advanced Tools
At Plastic Parts, Inc., we combine operator-led checks with real-time data capture and cutting-edge inspection tools to ensure consistent quality from press to pack.
- Operators follow detailed, part-specific visual instructions
- Defects are recorded in real-time through our ERP system
- A dedicated inspector verifies finished goods before shipment
Our advanced inspection tools provide the accuracy needed to validate dimensions, qualify mods, and verify part quality with confidence.
Mitutoyo CNC Vision Measuring System
Combines the strengths of a Coordinate Measuring Machine (CMM) with high-speed vision capabilities, enabling verification of tight tolerances and dimensional accuracy in complex parts.
Keyence 3D Scanner: We were the first company in the Upper Midwest to implement this advanced scanner, which enables full 3D part-to-CAD comparisons—ideal for mold qualification and tooling optimization.
AI-Powered Keyence Vision Systems: Dedicated to specific jobs, these state-of-the-art systems use machine learning for real-time inspection, continuously improving accuracy and catching issues before parts leave the press.
Ready to Elevate Your Quality Standards?
Whether you're designing a complex new part or seeking a more reliable molding partner, our team is here to help. Let’s discuss your specs and standards and how we can mold something great together.