Custom Injection Molding
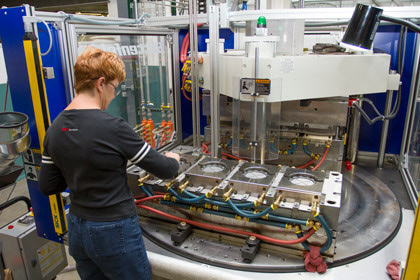
Injection molding is essential for producing high-quality, durable, and cost-effective plastic parts across a wide range of industries. Whether you need high-precision components for medical devices, lightweight solutions for automotive applications, or complex assemblies for industrial use, Plastic Parts, Inc. delivers tailored, high-performance injection molding solutions to meet your exact requirements.
With over 50 years of expertise, we combine cutting-edge technology, in-house tooling, and advanced molding techniques to optimize performance, reduce costs, and enhance product quality. From design and prototyping to full-scale production, we provide end-to-end manufacturing solutions that align with your specifications, industry standards, and production goals.
Why Choose Injection Molding?
Maintain exact specifications with repeatable accuracy.

Enhance production efficiency for small runs or large-scale manufacturing.
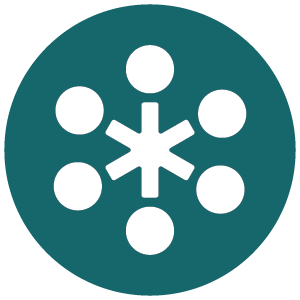
Short description or advantage for choosing injection molding.
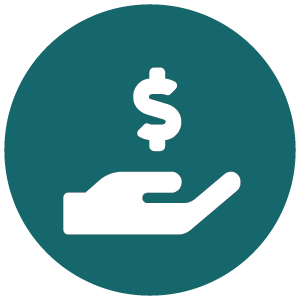
Reduce waste, minimize assembly steps, and improve manufacturing efficiency.
At Plastic Parts, Inc., we don’t just produce parts—we create custom-engineered solutions that ensure superior durability, functionality, and efficiency for your products.
Our Injection Molding Capabilities
We offer a full spectrum of injection molding solutions, integrating cutting-edge technology and proven engineering principles to design and fabricate custom molds that achieve superior results. Our expertise ensures precision, efficiency, and trusted guidance on material selection to optimize performance and durability for every application. As Solution Partners, we collaborate with OEMs to develop innovative, high-quality plastic components that meet industry demands.
Jump to a Section
Scientific Injection Molding
Scientific injection molding is a data-driven process that establishes and maintains optimal molding parameters to produce high-precision, repeatable, and defect-free parts. This method eliminates variability, ensuring consistency even in high-volume manufacturing. By carefully analyzing material behavior and processing conditions, scientific molding reduces defects, minimizes waste, and improves production efficiency.
Ideal Use:
- Automotive components where precision and consistency are critical
- Medical devices requiring exact tolerances and regulatory compliance
- High-volume manufacturing where repeatability is essential
- Electronics that require durability and reliability
- Telecommunications components that demand signal integrity
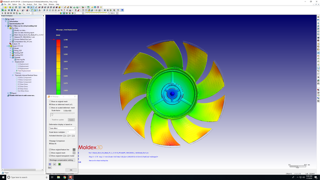
Insert Molding
Insert molding encapsulates metal, ceramic, magnets, or dissimilar resins within thermoplastic, creating a single, integrated assembly that enhances durability and functionality. This process eliminates the need for secondary fasteners or adhesives, improving strength while reducing overall part weight and size. Insert molding also enhances part longevity by increasing resistance to vibration, corrosion, and mechanical stress.
Ideal Use:
- Automotive electrical components requiring precise conductivity and insulation
- Medical devices with embedded sensors or electronic components
- Electronic connectors and switches needing precise alignment and durability
- Consumer products with hybrid material construction (plastic + metal)
- Industrial and aerospace applications requiring high-strength assemblies
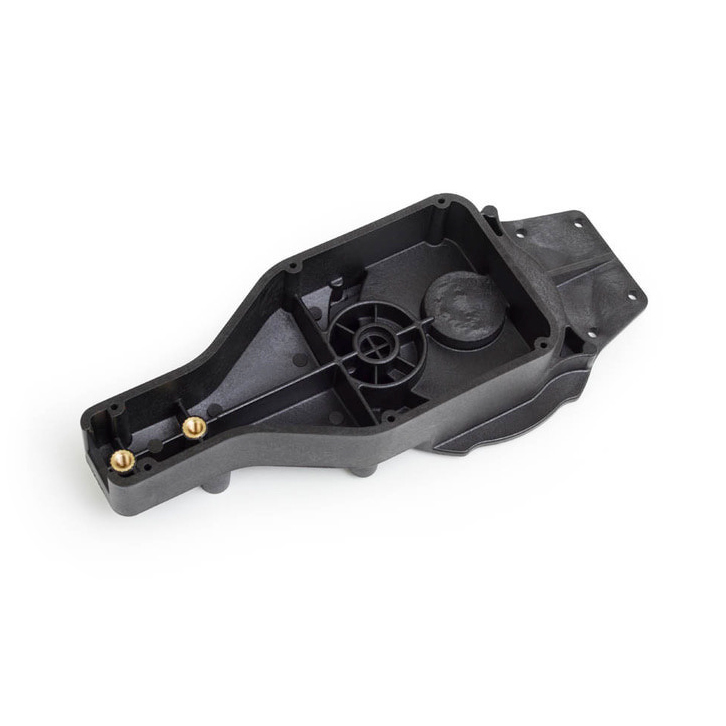
Overmolding
Overmolding is a thermoplastic encapsulation process in which one material is molded over another to create a durable, functional, and aesthetically enhanced product. This technique enhances grip, ergonomics, and durability, making it ideal for soft-touch surfaces and impact-resistant components. Thermoplastic encapsulation overmolding reduces the need for secondary operation and assembly, eliminates bonding, and increases product strength and heat and overload protection for a seamless, high-performance final product.
Ideal Use:
- Automotive interiors such as steering wheels and control buttons
- Medical devices with soft-touch grips for enhanced usability
- Consumer products like power tools, toothbrushes, and handheld devices
- Electronic housings and enclosures for better shock resistance
- Wearable technology and sports equipment for improved comfort and function
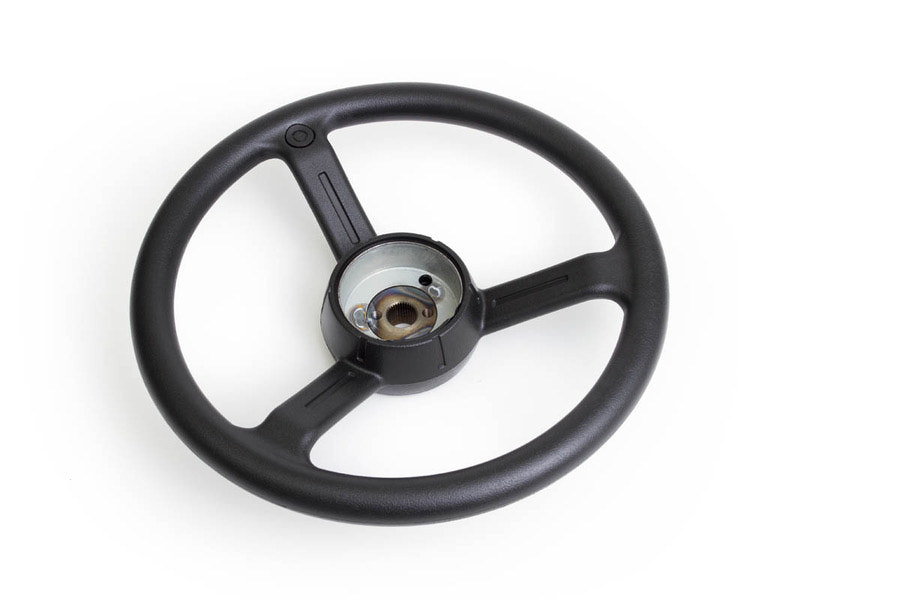
Gas Assist Injection Molding
Gas assist injection molding is an advanced technique that introduces pressurized nitrogen gas into the mold cavity, creating a gas pocket in thick sections to reduce material usage, increase strength, and improve processing efficiency. This method produces lightweight yet structurally sound parts while preventing sink marks, warping, and internal stress. The result is smoother surfaces, superior durability, and optimized performance. Applicable for most thermoplastic materials, gas assist molding is particularly useful where dense sections of plastic are needed.
Ideal Use:
- Automotive parts such as handles, panels, and seat frames
- Furniture components like chair arms and support structures
- Appliance housings that require reduced weight without sacrificing strength
- Medical equipment enclosures needing lightweight yet durable construction
- Industrial or outdoor equipment requiring structural integrity, like canoe or kayak paddles
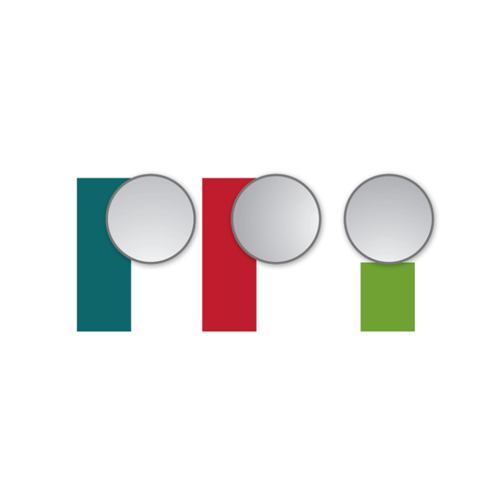
Plated Plastic Parts
Plastic plating enhances the wear resistance, corrosion protection, and aesthetics of injection-molded components by applying a range of metallic chrome finishes, including satin chrome, satin pearl, gold, and black sapphire. Plated plastic parts offer the look and performance of metal while being lightweight, flexible, and cost-effective, making them ideal for applications that require strength, durability, and a high-end finish without the added weight and cost of solid metal.
Ideal Use:
- Automotive trim and decorative parts requiring a high-end finish
- Consumer electronics needing enhanced durability and branding elements
- Medical device enclosures with protective coatings
- Industrial equipment requiring corrosion-resistant surfaces
- Household appliances and consumer products with metallic finishes
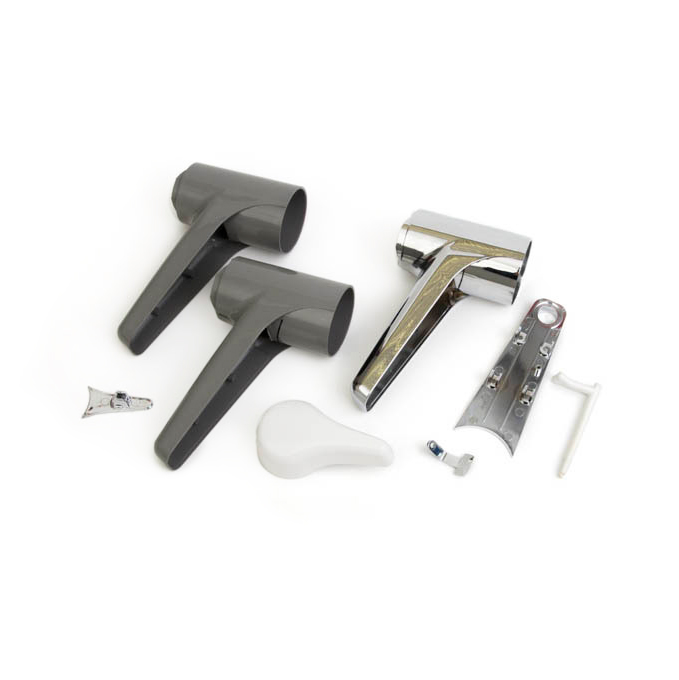
Why Choose Plastic Parts, Inc?
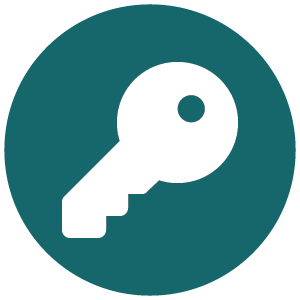
Turnkey Solutions for Injection Molding
We provide turnkey manufacturing solutions, ensuring a seamless transition from concept to production for manufacturers across various industries. Our comprehensive in-house process includes part modeling, mold design, prototyping, tool sourcing, production planning, quality verification, process control, decorating, secondary processing, and packaging. Our proven process maintains strict quality control and optimizes lead times and cost-efficient production, delivering precision-molded plastic components that meet or exceed industry standards.
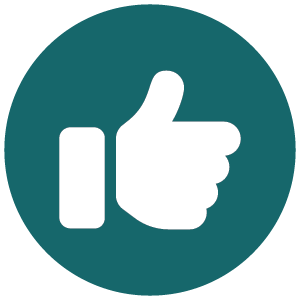
ISO-Certified Quality and Compliance
Plastic Parts, Inc. upholds the highest industry standards with ISO-certified quality control systems and UL-certified, FDA-compliant manufacturing practices, ensuring every component meets strict performance, safety, and regulatory requirements. Our rigorous testing and inspection process includes automated and manual quality checks to ensure precision and consistency. Our material traceability system delivers full adherence to industry specifications, providing complete documentation for quality assurance and regulatory compliance.
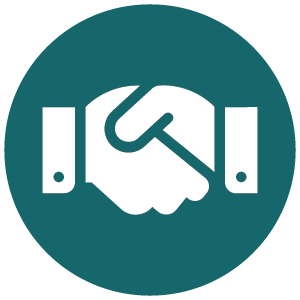
Trusted Expertise and Customer-Focus
For over 50 years, Plastic Parts, Inc. has been a trusted Solution Partner in precision-engineered injection molding for OEMs nationwide. We pride ourselves on working closely with manufacturers to analyze needs, develop solutions, and deliver high-performance products. Known for our comprehensive approach, we leverage expert design consultation, technical assistance, and production support to ensure best-in-class plastic components. Our commitment to innovation and service excellence is behind every product we manufacture.
Let’s Mold Something Great Together
Looking for a trusted Solution Partner in high-quality injection molding? Fill out the form below to discuss your project, request a quote, or get expert guidance from our team. We’ll be in touch soon!